Plastic extrusion for pipes, sections, and custom shapes
Plastic extrusion for pipes, sections, and custom shapes
Blog Article
A Comprehensive Overview to the Process and Benefits of Plastic Extrusion
In the large realm of manufacturing, plastic extrusion becomes a very efficient and necessary procedure. Altering raw plastic right into constant accounts, it caters to a wide variety of sectors with its exceptional versatility. This overview intends to elucidate the complex steps entailed in this method, the kinds of plastic proper for extrusion, and the game-changing benefits it brings to the sector. The taking place discussion assures to unfold the real-world influences of this transformative procedure.
Comprehending the Essentials of Plastic Extrusion
While it might show up complicated in the beginning glimpse, the process of plastic extrusion is basically easy - plastic extrusion. It is a high-volume manufacturing technique in which raw plastic is melted and shaped right into a continuous profile. The process begins with the feeding of plastic material, in the form of pellets, granules, or powders, into a heated barrel. The plastic is after that melted utilizing a combination of heat and shear, applied by a turning screw. When the molten plastic reaches the end of the barrel, it is compelled via a tiny opening recognized as a die, shaping it into a desired kind. The designed plastic is then cooled, strengthened, and reduced into wanted lengths, completing the process.
The Technical Process of Plastic Extrusion Explained

Types of Plastic Suitable for Extrusion
The choice of the appropriate type of plastic is an essential aspect of the extrusion process. Numerous plastics supply unique residential or commercial properties, making them a lot more matched to specific applications. Polyethylene, as an example, is typically utilized because of its inexpensive and easy formability. It provides excellent resistance to chemicals and dampness, making it perfect for products like tubing and containers. Polypropylene is an additional prominent selection due to its high melting point and resistance to tiredness. For more robust applications, polystyrene and PVC (polyvinyl chloride) are commonly selected for their stamina and toughness. These are typical options, the selection eventually depends on the particular requirements of the item being created. Recognizing these plastic types can significantly improve the extrusion procedure.
Comparing Plastic Extrusion to Various Other Plastic Forming Methods
Understanding the kinds of plastic suitable for extrusion leads the method for a wider conversation on exactly how plastic extrusion more information stacks up versus various other plastic creating methods. Plastic extrusion is exceptional when it comes to creating continuous accounts, such as seals, pipes, and gaskets. It also allows for a consistent cross-section along the length of the product.
Key Benefits of Plastic Extrusion in Production
In the world of production, plastic extrusion supplies numerous significant advantages. One significant advantage is the cost-effectiveness of the process, that makes it an economically appealing manufacturing approach. Additionally, this strategy offers remarkable product versatility and enhanced production rate, therefore raising total production effectiveness.
Cost-Effective Production Technique
Plastic extrusion jumps to the leading edge as an affordable production method in manufacturing. Furthermore, plastic extrusion calls for much less energy than traditional production techniques, contributing to lower operational expenses. Generally, the financial advantages make plastic extrusion a highly eye-catching choice in the manufacturing sector.
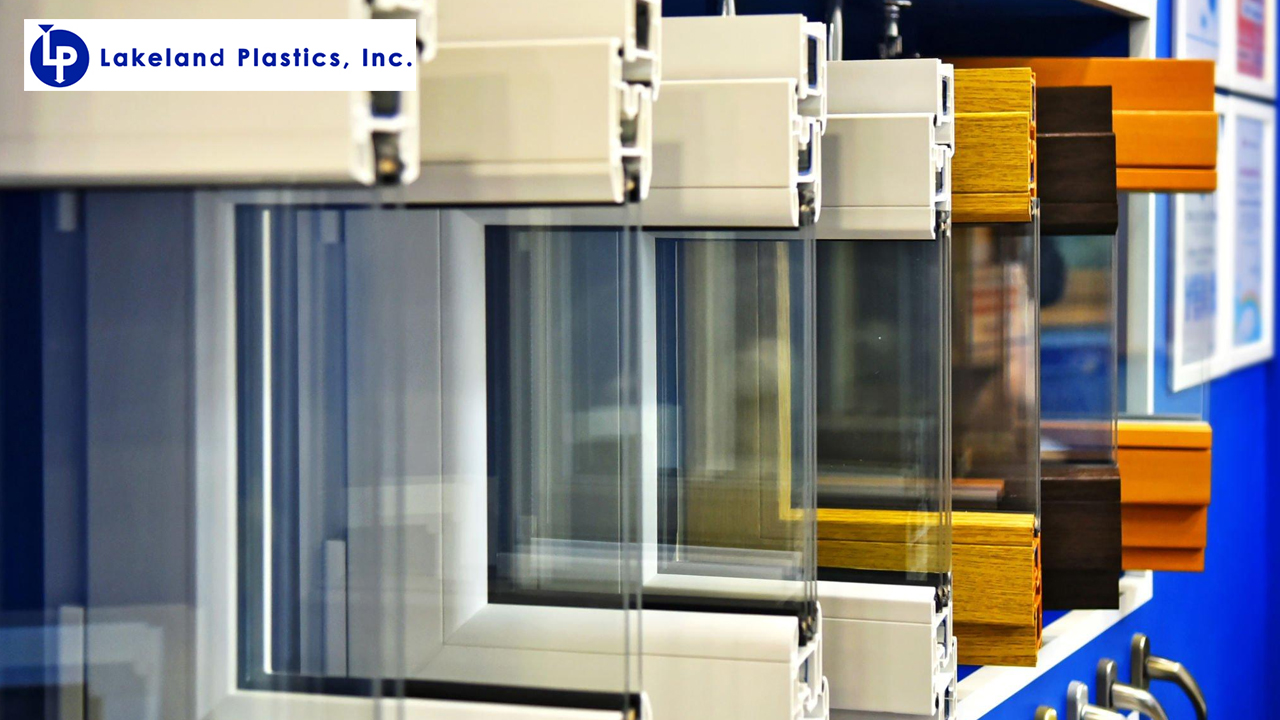
Superior Item Flexibility
Past the cost-effectiveness of plastic extrusion, another considerable benefit in manufacturing lies in its remarkable item versatility. This makes plastic extrusion an excellent service for markets that require personalized plastic parts, such as automobile, construction, and product packaging. In significance, plastic extrusion's product versatility cultivates development while boosting functional efficiency.
Improved Production Rate
A substantial benefit of plastic extrusion hinges on its her comment is here enhanced production rate. This manufacturing procedure permits high-volume production in a relatively brief time period. It can generating long, constant plastic profiles, which substantially minimizes the production time. This high-speed production is particularly useful in markets where large quantities of plastic components are needed within limited due dates. Few other production processes can match the speed of plastic extrusion. In addition, the capacity to preserve regular high-speed production without giving up item high quality sets plastic extrusion in addition to various other techniques. The enhanced production rate, for that reason, not just makes it possible for producers to meet high-demand orders but also contributes to increased performance and cost-effectiveness. This useful function of plastic extrusion has made it a favored choice in various industries.
Real-world Applications and Effects of Plastic Extrusion
In the realm of manufacturing, the strategy of plastic extrusion holds extensive relevance. This process is widely made use of in the manufacturing of a range of products, such as plastic tubes, window frameworks, and climate removing. Because of More Help this, it greatly influences markets like building, packaging, and auto markets. Moreover, its influence reaches day-to-day items, from plastic bags to tooth brushes and disposable flatware. The financial advantage of plastic extrusion, mainly its high-volume and cost-effective outcome, has transformed manufacturing. Nevertheless, the environmental impact of plastic waste stays a worry. Consequently, the industry is constantly striving for technologies in recyclable and naturally degradable materials, suggesting a future where the benefits of plastic extrusion can be maintained without jeopardizing ecological sustainability.
Final thought
Finally, plastic extrusion is a efficient and highly effective method of changing resources into varied products. It offers various advantages over other plastic creating techniques, including cost-effectiveness, high result, minimal waste, and layout adaptability. Its effect is greatly really felt in different markets such as building, auto, and durable goods, making it an essential process in today's manufacturing landscape.
Diving much deeper into the technological process of plastic extrusion, it starts with the option of the proper plastic product. Once cooled, the plastic is reduced into the required sizes or wound onto reels if the item is a plastic film or sheet - plastic extrusion. Comparing Plastic Extrusion to Various Other Plastic Forming Techniques
Recognizing the types of plastic suitable for extrusion leads the way for a wider conversation on exactly how plastic extrusion stacks up against various other plastic developing methods. Few other manufacturing procedures can match the rate of plastic extrusion.
Report this page